By Chris Demeter, Sr. Loss Control Representative
If I inspect a tool & die shop, I would more than likely find at least one bench or pedestal grinder. If you went into my garage, you would find a pedestal grinder that comes in handy when I need to sharpen my lawnmower blades, mine has three. These grinders come in many styles, sizes, and designs. Typical bench and pedestal grinders often have two abrasive wheels, or one abrasive wheel, and one specialpurpose wheel such as a wire brush, a buffing wheel, or a sandstone wheel.
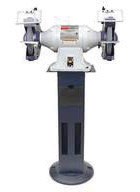
Grinders operate at very high speeds – the wheels often rotate at several thousand RPMs. If a grinding wheel shatters while in use, the fragments can travel more than 300 mph, so there’s a risk for serious injury from flying fragments and the rotating wheel assemblies (including the flange, spindle end, and nut). Abrasive wheels used on bench and pedestal grinders must be equipped with safety guards. The safety guard encloses most of the wheel — covering the flange, spindle end, and nut projection — while allowing maximum exposure of the wheel periphery. The exposed surface of the wheel should not exceed 90 degrees or one-fourth of the periphery.
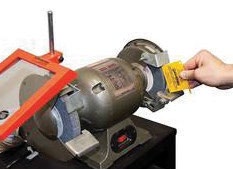
Because the safety guard is designed to restrain the pieces of a shattered grinding wheel, the distance between the safety guard and the opening at the top of the wheel must not be more than 1⁄4-inch. If the distance is greater than 1⁄4-inch, then an adjustable “tongue guard” must be installed to protect workers from flying fragments if the wheel shatters. The tongue guard must be adjusted to maintain a maximum 1⁄4- inch distance between it and the wheel. An adjustable work rest must also be installed and adjusted to maintain a maximum clearance of 1⁄8-inch between it and the wheel. This prevents the operator’s hands or the work from being jammed between the wheel and the rest.
All abrasive wheels must be inspected and “ring-tested” before they are mounted to ensure that they are free from cracks or other defects. Wheels should be tapped gently with a light, nonmetallic instrument. A stable and undamaged wheel will give a clear metallic tone or “ring.” It’s a good idea for the operator to stand to the side of the machine when powering it on in case a crack or defect was not detected when the wheel was inspected. If the wheel happens to shatter, the particles will be less likely to strike you. The spindle speed of the machine must also be checked before mounting the wheel to be certain that it does not exceed the maximum operating speed marked on the wheel. Abrasive wheels used on bench and pedestal grinders must be equipped with safety guards.
The OSHA standard for grinders, OSHA 29 CFR 1910.215, is one of the most frequently cited violations issued during a MIOSHA safety inspections. Improperly adjusted work rests and tongues on the grinder are the main reasons for the citation. Abrasive wheel grinders are great machines, but careless operation can injure your hands, fingers, eyes, and respiratory system. The fact that OSHA finds so many abrasive wheel grinder violations every year should be a warning to all of us. Remember that the most common violations—and serious hazards—are failing to properly adjust the safety guards and the work rests. A wheel that fragments at high speed can cause severe personal injury and possibly death.
Lastly, make certain you have no loose-fitting clothing, gloves, jewelry, hair, or other items dangling as you operate the grinder or any other rotating equipment. If one of those things gets tangled up in the revolving grinder wheel, an injury is almost certain to occur. I always recommend posting signs out in the shop as a visual reminder. “Due to the possibility of entanglement, gloves, loose clothing, jewelry, and long hair should never be worn while operating any rotating device.”
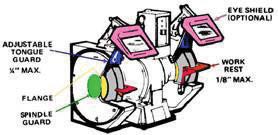
If you have a question about these precautions to take when operating a pedestal or bench grinder, please be sure to contact your Loss Control consultant.