By Travis Halsted, ARM, COSS, Loss Control Consultant
The Future is Here
As we look outside every morning, we see that the weather is improving, and we are starting to shake that cabin fever. The sun hits our faces on the way to work, and optimism fills us for the upcoming day. Regardless of the industry that you work within, most of us are all met with the same issue once we arrive in our parking spots. That issue is simply people, or the lack thereof. The ability to not only find people willing to work, but to secure them for a period of time that extends past the first day is quite a feat as of late. Very few places have been able to combat this issue, but some of the manufacturing facilities have found a possible resolution. This resolution is simply re-placing the position in which an employee would be with a collaborative robot, or often referred to as “cobots”. As labor costs continue to rise, as does the need for flexibility in automation, mixed with the aforementioned shortage of qualified workers, employers are finding these cobots to not only be an option, but more so as their only option. The sales of these robots had grown to $400 million in 2017 but is expected to climb as high as $7.5 billion by the year 2027.
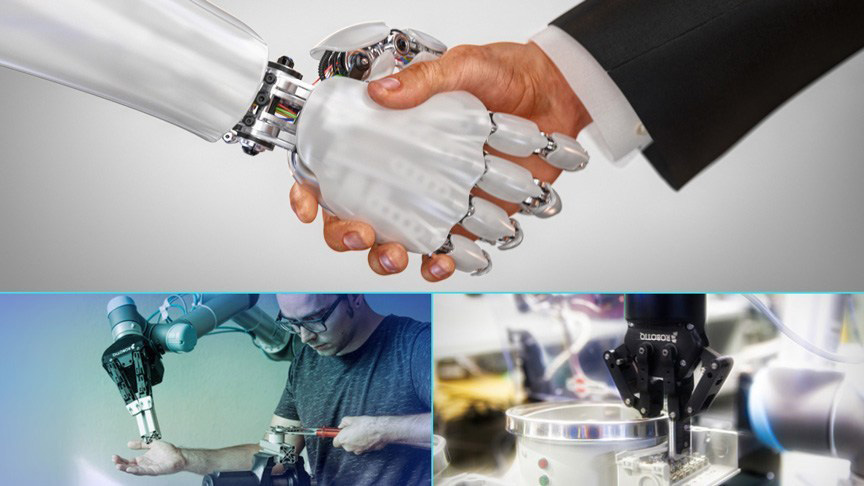
For those of you that may not be familiar with the term collaborative robot, it is simply a power and force limited robot that is equipped with very accurate and safety force sensing capabilities. These cobots work within a defined area, and will stop if they encounter an unexpected force, such as bumping into a person or piece of equipment. This stopping capability allows these robots to work side by side with humans. These cobots are usually focused on repetitive tasks such as inspection and picking/placing but can have attachments to load/unload parts to/from machinery, conduct welding operations, and even assist in painting/powder coating. As these forms of robotics have grown, it could be assumed that there would be a plethora of rules regarding them. Surprisingly, that is not the case.
Lack of Standards
Federal OSHA, as well as MIOSHA do not have a robotics standard per se, but instead lean on the subparts that pertain to the processes in which the robot is completing. For instance, a great deal of robotics violations pertain to the proper lockout/tagout procedures that one would complete while working with the energy sources for a collaborative robot. Other MIOSHA areas that are cited when working with collaborative robots include, but are not limited to, mechanical power presses, abrasive wheel machinery, welding operations, and even woodworking machinery. It is vital that we do not only look at the robot itself, but also the processes that the robot is working with. While OSHA/MIOSHA may not have set rules for collaborative robots, other agencies such as, ISO (International Organization for Standardization), ANSI (American National Standards Institute), and RIA (Robotics Industries Association) all have National Consensus Standards for robotics that provide guidance to OSHA/MIOSHA during an inspection/investigation. For instance, ISO/TS 15066:2016 discusses numerous items regarding collaborative robots that allows an enforcement official the ability to cite for if found not to be compliant. One of those items, and possibly the largest aspect of a collaborative robotics safety program, is the requirement for a risk-based assessment.
Risk Assessments
While collaborative robots are designed to work safely with close human interaction, this risk-based assessment is still required for each robot and each task that the robot will be completing. This risk assessment is aimed at considering all ways in which the operator may be exposed to a hazard such as pinch points and entanglements with end of arm tooling. Upon identifying each process, you must break down the risk down into categories of degree of possible harm (severity), the frequency of exposure, and the possibility of avoidance.
- Injury Severity – The injury severity is broken down into three ratings. These ratings are serious, moderate and minor. Serious can range from fatality, amputation, long term disability and chronic illness. Moderate can include fractured bones, lost time, severe lacerations and short hospitalizations. Finally, minor can include bruising, small cuts, no loss time, and does not require attention by medical doctor.
- Exposure – The exposure category is broken down into prevented, high and low. While injury severity rating names are, for the most part, self-explanatory, these are not as simple. Each of these have an in-depth explanation as to how frequently the operator would be in the hazard zone, the duration in which the operator would be in the hazard zone, and whether the task is routine, or non-routine.
- Avoidance – The avoidance category determines how easily an operator can sense and elude a hazardous situation. This category covers items such as clearance distances, speed and ergonomic characteristics of the hazard zone, and even potential hazardous materials within the hazard zone.
Once all of these items have been evaluated, a risk level is determined for each task with the categories above. From there, a hierarchy of risk reduction methods can be used to reduce the risk to obtain what is deemed as an acceptable risk. After all of that, verification of the risk reduction, validation of that same risk reduction, and the documentation of it must be done as well. While this all seems like a great deal of work, you may be surprised at how quickly it will go.
For assistance in identifying the hazards that your robot(s) may have, or how to conduct the risk assessment, please reach out to your MTMIC Loss Control Consultant. As controlling losses is heavily based on the “what ifs” in a workplace, we can assist in dissect-ing the operations for the different exposures within the processes. I hope that 2023 has been a healthy and successful year for all of you!